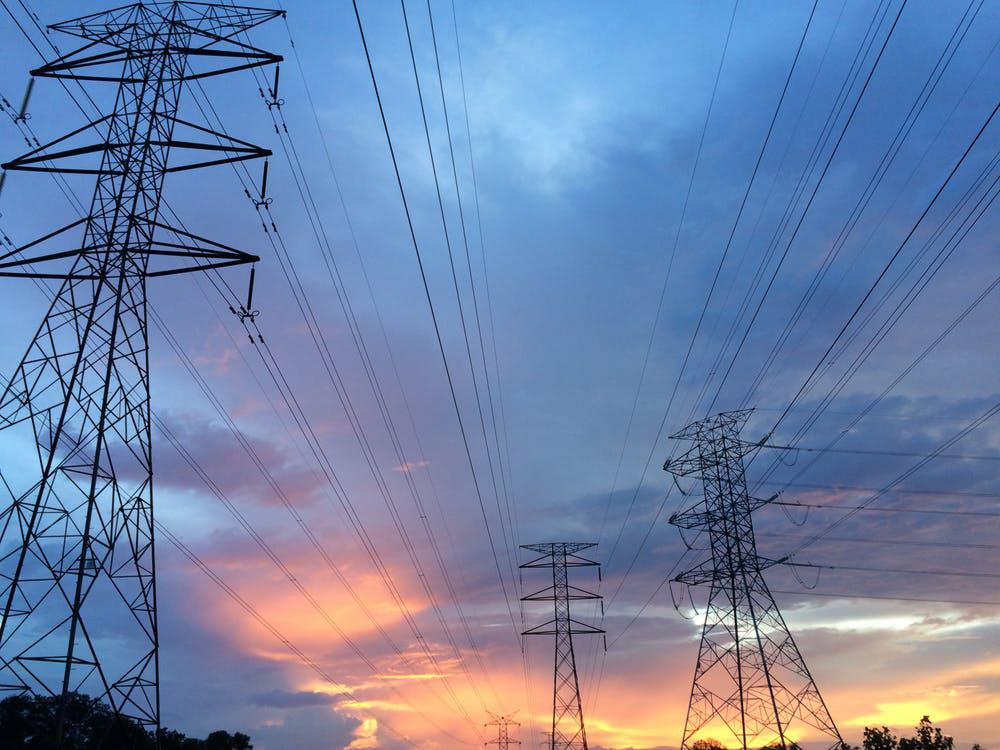
Understanding the Electricity Safety Tests
It is critical to guarantee safe operating standards for any products that employ electricity. This is the reason why electrical safety testing is conducted. Unfortunately, not all manufacturers and consumers completely understand the importance of proper electrical safety testing.
You have to know that you are at risk of shock hazards. Shock hazards can cause mild tingling sensations to fatal jolt. With this, it is crucial that shock hazards are identified, corrected and eliminated. To ensure electrical safety, there are many tests that should be done for a product to pass. In general, the widely accepted standard for electrical safety is IEC 60335. This is especially the standard for domestic appliances. Here are some electricity safety tests:
What is a high voltage test?
This is also called dielectric voltage-withstand test. The hv test is a must for all electrical products. This means that every unit should pass it before it can be used. In this test, a higher voltage is applied. The voltage applied should be higher than the operating voltage because it will test the insulation of a specific product. The product, if stressed to greater levels should not be breached.
What is the insulation resistance test?
The insulation resistance test is done to assess the total resistance of a specific product’s insulation by applying 500 to 1,000 voltage. The acceptable value for a product to pass this test is 1 megohm. However, this test is not an alternative to a high voltage test. Remember that every electrical unit should pass a high voltage test before it can be used.
What is earth continuity test?
In this test, it can measure the resistance between the outside metal body of a specific product and the third pin or ground. The acceptable value is 0.5 ohms. This test is important to ensure that a particular product does not result to an electric shock.
What is the leakage current test?
This is also called line leakage test. The test will measure the leakage current that runs within the surface of the capacitor. The acceptable limit of leakage is 210 microamperes. First, there will be a visual inspection. At this point, the electrician will survey the installation before the electrical testing. Through visual inspection, the electrician can identify cracked or broken devices.
After that, there will be electrical testing using dead testing and live testing. Dead testing includes the following types of testing: continuity testing (which is used to check if there are badly connected wires or conductors), insulation resistance testing (which is used to ensure that electrical insulations are intact), polarity (which is used to test if the connection is connected right) and earthing arrangement testing (which is used to ensure that earthing arrangement conforms with regulations).
Live testing includes earth fault loop impedence testing (which is used to test if faults happened) and RCD testing (which is used to test the reaction to electricity missing from the circuit). The electrician will then issue a Periodic Inspection and Testing Report describing the observed damage, defects, condition, and non-compliance.